冲压模具实现自动化的几个方向
模具技术水平的高低是衡量一个国家制造业水平高低的重要标志,随着我国工业进一步的发展要求模具行业向大型,精密,高效,多功能方向展,其中一个重要的途径是将模具与自动化结合,本文结合冷冲压模具领域经验及自动化技术,共同探讨冲压模具发展方向。
一.冷冲压模具发展现状
冲压模具的发展关键是模具制造技术,模具材料及模具人才。模具技术的发展是模具工业发展的一个关键因素,其发展目标是适应模具产品交期短,精度高,质量好,价格低的要求,其中一个重要的方向是大力发展模具自动化。冲压模具相关自动化开发是将传统模具与光机电技术结合,将多制程的自动化模组集成在模具内,通过电气控制,实现全连续模生产,从而节省大量机台和人力,达到效率最大化,制程最优化,效益最大化
二.冲压自动化生产的优势
冲压加工是指在冲床上安装模具,将板状的材料通过模具之间时,冲压力使材料变形,切断,弯曲,成型等的加工,可以实现自动化加工的冲压工艺有:五金件铆接,攻丝,产品自铆互铆,小组件集成生产。
冲压工艺因其互换性好,节省材料,有其他加工方法难以制造的壁薄,重量轻,刚性好,表面质量高,形状复杂的零件,在市场上有极广泛的应用,但目前较多数的冲压模具生产都采用手动的方式,极大的制约了其发展。
手动冲压加工的问题点有:
1.冲压加工属重体力作业,且具有一定的危险性,造成冲压企业招工难;
2.手工冲压需要作业空间大,半成品的存量大,新冲压及模具技术的未及时导入,造成实际生产时效率低,成本高;
3.手工冲压因设备故障或人身因素引发安全伤害事故,冲压自动化生产线很大程度上弥补了上述不足,随着电子产品少量多样时代的到来,再加上招工难用工贵等因素影响,冷冲压领域自动化发展是其必然要求。
三.冲压自动化生产技术发展实例
1.模内铆螺柱技术
(1)传统铆螺柱技术:采用连续模下料,人工将螺柱放入产品,再由工站模进行铆合。此生产方式需要较多机台和人力,劳动强度大,效率低。
(2) 创新型模内铆螺柱技术:该技术采用振动盘和直振将螺柱有序排列,进入分料杆前端,上模插刀驱动分料杆一次导引1PCS螺柱,被分料后的螺柱在气的作用下经轨道送至模具内部铆合点,进入待铆合状态。铆合时,夹紧滑块先夹紧螺柱,对螺柱精确定位,模具在下行过程中,浮升铆合冲头下行,叉刀驱动侧滑块向两边运动,夹紧滑块分开。浮升铆合冲头运动到位后,上模继续下行,铆合冲头驱动螺柱完成铆合,实现全连续模生产。
铆螺柱结构示意图
2.模内伺服攻牙技术
(1)传统攻牙技术:采用连续模下料,人工将产品放入台式攻牙机进行攻牙。此生产方式需要较多机台和人力,劳动强度大,效率低。
(2)创新型伺服模内攻牙技术:该技术采用伺服电机驱动,高精度齿轮传动,万向节连接齿轮轴和牙杆轴。下模采用活动脱板结构,上模下行先压料再攻牙。牙杆设计快换式夹紧机构,可快速更换丝锥。整个攻牙模组结构紧凑,可全部集成在下模内,拆卸维修快速方便。万向接结构,攻牙轴位置可随意调整,通用性强。模内最多可同步攻牙20PCS,产能可达2000PCS/小时,实现全连续模生产。
伺服攻牙结构示意图
3.模内铆合,贴胶集成技术
(1)传统铆合,贴合技术:采用连续模下料,工站模人工放螺柱进行铆合,再由人工贴胶。此生产方式需要较多机台和人力,劳动强度大,效率低。
(2)创新型模内铆合,贴胶集成技术:该技术首先将模内铆螺柱模组集成在连续模具内,贴胶模组包含上料机构,剥胶机构,贴合机构,收料机构,电气控制。整个模组独立快拆,方便维修。上料机构置于模具前端,便于更换料卷。动力采用伺服控制,运行稳定可靠。贴合机构设计一模三穴,匹配模具产能,实现全连续生产,产能可达1800PCS/小时。
集成模组结构示意图
4. 多料带铆合技术
(1)传统多产品互铆技术:多产品互铆通常先用几套模具分别将产品单件生产出,再由人工将产品组合在一起,用工站模进行铆合。此生产方式需要较多机台和人力,劳动强度大,效率低。
(2)创新型多料带铆合技术:该技术是将多个产品集成在一套模具内完成,根据产品铆合方式,分别设计平行送料和垂直送料。平行送料由冲床自带送料机完成,垂直送料由两组微型气动送料机构完成,送料机构1在前端拉料,送料机构2实现精准送料。需铆合的产品由料带或输送机构送至铆合位置,上模下行进铆合,最后产品切断出料。该技术实现了多产品全连续模生产,产能可达2000PCS/小时。
多料带铆合结构示意图
经过多年的实践探索,冲压自动化生产已取得可喜的成果,通过生产导入,带来可观的经济效益,工业是立国之本,强国之基。而模具作为工业之母,其地位之重要可想而知。目前国家大力落实推动制造业升级发展,模具向自动化方向转型是必由之路,给模具插上智慧的翅膀,将显着提升企业提升在行业内的核心竞争力。
汽车人专业群:汽车主机厂及一级供应商高质量技术交流群,宗旨:学习交流,信息分享,加下方小编微信入群,入群说明:专业群
本文来源:网络,版权归原作者所有。
编辑整理:小D
商务合作:15021024736
投稿邮箱:gsmidesign@163.com
识别下方二维码加小编微信;加QQ群直接进入,招募QQ群管理。
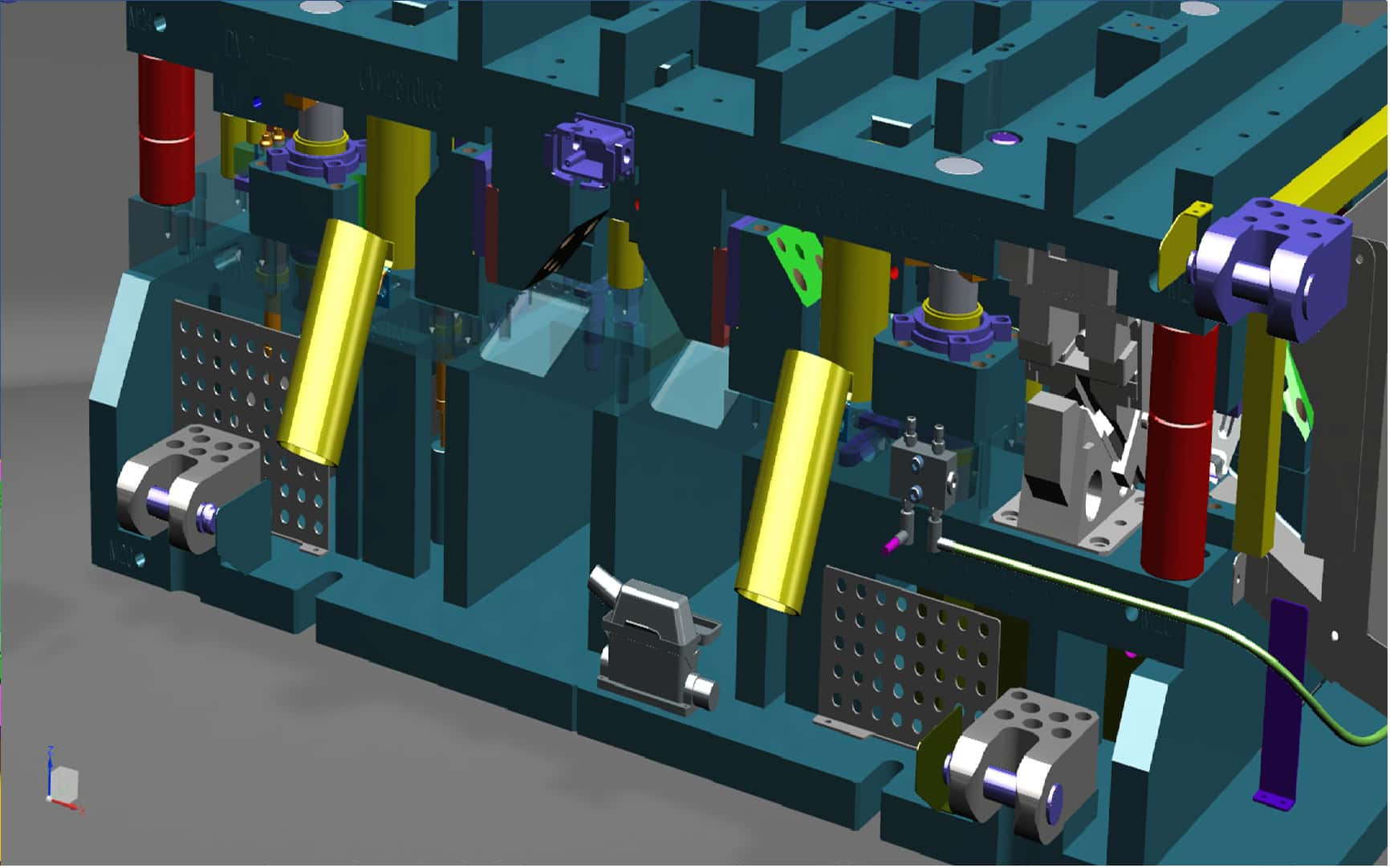